Testing the Bond Strength of RAPID Devices
ABSTRACT
Cancer is a prevalent issue that causes thousands of deaths annually. Many deaths could be prevented by early identification. A primary identification method is a PET (Positron Emission Tomography) scan. PET scans use radioactive drugs called radiotracers to collect in, and highlight, cancerous tissue. There are many unique radiotracers that can effectively identify specific cancers. Unfortunately, the current production pipeline favors only one radiotracer, fluorodeoxyglucose, and makes other, more specific radiotracers unaffordable. A solution is the development of a platform that uses microfluidic devices, known as RAPID, to synthesize radiotracers affordably and on-demand. In microfluidics, the bond strength of a device is crucial for its functioning. RAPID (Radiopharmaceuticals as Precision Imaging Diagnostics) are microfluidic devices that synthesize radiotracers affordably in single doses. In this study the bond strength of RAPID devices was tested under different fabrication procedures, operating conditions, and ethanol exposures to maximize its efficiency. This was done through burst tests using the pressure at which the device bond failed as a gauge of bond strength. The results were that the fabrication procedure is within a robust window, clamping the fluidic interface minimally increases fluid pressure capacity, and ethanol exposure weakens the bond strength of RAPID devices.
INTRODUCTION.
Cancer is a disease caused by rapid and uncontrollable cell growth in the body that can lead to severe and potentially fatal health issues. Cancers are usually deep within the body and require internal imagining to be identified. A commonly used method by doctors to identify cancers is PET (positron emission tomography) scans. PET scans are a medical imaging technique that utilize radioactive drugs known as radiotracers to detect diseases in the body. Radiotracers are an integral component used in PET scans and are extremely important in identifying cancerous tissue. Over 4000 unique radiotracer probes exist and are highly effective at identifying specific cancers [1]. Fluorodeoxyglucose ([18F]FDG), an extremely common radiotracer used in 95% of procedures, is a radiolabeled glucose molecule that dominates the radiotracer market [4]. The broad effectiveness of this radiotracer to identify tumors and its development as an early radiotracer has caused the current production pipeline to favor the synthesis of large quantities of [18F]FDG. However, due to it being a glucose-based molecule and the constant metabolism of glucose in the body, [18F]FDG is not highly selective when identifying tumors and can lead to “false positives” [1]. Thus, cancer identification in its earlier stages is made difficult due to the unaffordability of more specific radiotracers, known as boutique radiotracers, because of the current production pipeline. A more efficient production pipeline system is needed to address the problem radiotracer production faces.
Microfluidics provide a solution to the radiotracer production pipeline. A study in 2005 successfully synthesized the radiotracer [18F]FDG using a microfluidic device [2]. This opened the door for a device known as RAPID that addresses the issues with the radiotracer production pipeline model (Figure 1) [1]. RAPID can synthesize a wide range of radiotracers in single batch doses that can be produced based on demand. The device is simple and easy to produce as well as cheap. It is similar to a device developed by Zhang that uses photolithography [3], [4]. However, this device uses stereolithography, making it cheaper, easier, and faster to produce. It contains all essential steps used in previous research for synthesis of radiotracers using microfluidics. The device is made of a PDMS substrate bonded to a glass slide and includes a microreactor, purification column, concentration column, and mixing channel [1]. A fully finished RAPID device would feature both columns filled with unique resins to facilitate the purification and concentration steps. This device would be incorporated into a platform, that together could synthesize many unique radiotracers. As development of this device continues, its limits and safety need to be tested.
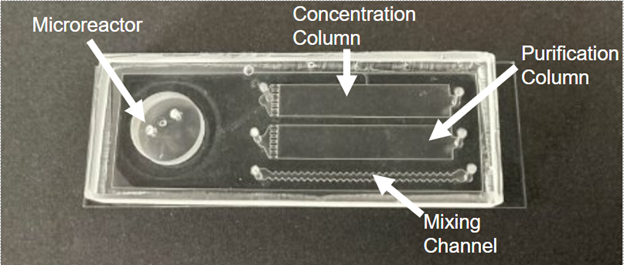
An essential component of RAPID is the bond that creates a tight seal between a glass microscope slide and the substrate PDMS. This seal allows for the passage of fluid through the device and synthesis to occur. Greater bond strength allows for higher fluid pressure capacity and thus more fluid to be passed through the device without it bursting. Therefore, the limits of RAPID device bond strength needed to be tested and optimized to ensure the efficiency of the device. A study in 2005 found that the surface wettability of PDMS and glass was affected most by oxygen-plasma exposure time [5]. This condition is easily manipulable during the fabrication procedure and shows promise in optimizing the bond strength of RAPID devices. Additionally, RAPID devices have never been previously tested under operating conditions before, and an operating range needs to be developed to ensure safety and efficiency. These conditions included a fully packed column with resin, a microfluidic interface, and physical pressure on the device.
An unexpected difference between the results of the two experiments mentioned above led to the addition of a third experiment. The devices tested under operating conditions burst at lower fluid pressures than the devices tested under different fabrication parameters. After considering that devices tested under operating conditions were exposed to ethanol and devices tested under different fabrication parameters weren’t, the connection between bond strength and ethanol was made. A study conducted in 2018 identified the extent of swelling that commonly used solvents like ethanol have on thin polymer films like PDMS [4]. This swelling could be a factor leading to the difference in the results of the two experiments. Although it is already known that ethanol causes PDMS to swell, it is not known how much this affects the bond strength of microfluidic devices.
It is hypothesized that increasing O2 plasma exposure time will increase surface activation, thus surface wettability, yielding a stronger bond. Increasing the physical pressure applied to a device will increase its fluid pressure capacity due to the facilitation of a tight seal around the tubes preventing leakage, and the physical support it receives. Finally, ethanol exposure will weaken the bond strength of RAPID devices due to the swelling of the PDMS substrate.
MATERIALS AND METHODS.
RAPID Fabrication Procedure.
The Fabrication of RAPID devices follows a 7-step procedure that creates a fully finished product used for radiotracer synthesis. The procedure used in this study is similar to the procedure used in a study by Zhang in 2020 but uses stereolithography (SLA) printing instead of photolithography to make molds [3]. First a 3D mold was printed for device fabrication using SLA. During this step, the base layer of the mold was exposed to UV light for 5 seconds to create a smooth surface. The mold was designed on a computer using a computer program known as Fusion Cad. The virtual model file was uploaded to an SLA 3D printer and a mold was printed. Then, the mold surface was coated with a layer of parylene. This was done to create a protective layer on the mold that would prevent scratches and uneven bonding sites. Next, the RAPID device chip was cast using a PDMS substrate made of PDMS elastomer base and curing agent. This cast was placed into an oven overnight and was heated at 80 °C. Then, the PDMS chip was released from its mold. After this was complete, holes were punched into the chip to allow for tube access using a hole punching machine. Additionally, a glass microscope slide was prepared for bonding by cleaning its surface using deionized water. The surface of the PDMS chip and the glass microscope slide were then activated using an O2 plasma cleaning vacuum chamber and pure oxygen. This step excites the surface of the PDMS and glass allowing the bond to take place. Immediately after, the PDMS and glass were bonded by pressing the materials together using light pressure. The bond was strengthened by heating the device for 15 minutes in an 80 °C oven. For devices requiring packed columns during testing, resin was packed into both columns by pumping a 70 percent ethanol solution, containing C18 silica sphere mono beads (resin), through the device until the column was full (10 to 15 minutes).
Varying O2 Plasma Exposure.
The bond strength of RAPID devices was tested using the maximum fluid pressure capacity (psi) of a device as a gauge of bond strength, these were known as burst tests. This was done using a fluid pressure sensor attached to a tube protruding from the device columns. During the PDMS and glass activation step, the O2 plasma exposure time in the O2 plasma cleaner was manipulated. The amount of time the device was exposed to O2 was increased and decreased in an attempt to increase device surface activation (increased time) but not cause over activation (decreased time). 3 different O2 exposure times were tested: 15, 30, and 45 s. Similarly, 3 devices of each condition were fabricated and tested. Finally, each device was left unpacked to more clearly see the direct effect of each parameter on bond strength
Simulation of Varied Operating Conditions.
The RAPID device was developed for use inside of a mechanical platform and will be subject to forces of physical pressure, fluid pressure, and connection to a fluidic interface. These conditions were simulated during burst tests to test the bond strength of these RAPID devices. This experiment repeated the burst test procedure followed in experiment 1 with modifications to the forces exhibited onto the device. To develop operating conditions, a set amount of force in pounds (lbs), Using 2 Westward 2FDC5 hand clamps, was exhibited onto the RAPID device. A fluidic interface was developed using a system of microbore tubes attached to the entrances and exits of the device column, with a 3D printed cap compressing gaskets around the tubes evenly. Pressure from the hand clamps on these gaskets facilitated a tight seal that would be normally experienced under operating conditions. Finally, columns were packed with resin to mimic the conditions experienced during operation. In addition to the development of operating conditions, the clamp force exerted on the device was varied for each test to determine the optimal pressure needed for an optimal gasket seal. 3 tests were conducted at each set clamp force: 0, 0.92, 8.10, 15.3, and 25.4 lbs. Additional tests were also conducted to determine at which clamp force the devices integrity failed without the flow of fluid through a device column. This was done by continually increasing clamp force on a device until the device broke at a certain number of pounds of force.
Varying Ethanol Exposure.
Ethanol is known to swell PDMS and could potentially weaken the bond strength of RAPID devices [6]. Unfortunately, ethanol is an essential component of the packing procedure that allows for resin to enter the device columns and cannot be removed. The bond strength of RAPID devices while being exposed to ethanol was tested. For this experiment, the burst test procedure was repeated with the substitution of ethanol as the fluid being pumped through the device column instead of pure water. Additionally, device columns were left unpacked to eliminate extra fluid pressure buildup generated by the presence of resin in the device column. This test was conducted 3 times.
RESULTS.
Varying O2 Plasma Exposure Results.
For O2 plasma exposure time, 3 tests were conducted for each O2 exposure time parameter and the psi at which the device burst was recorded with the exception of the 45s-time parameter with 4 tests. Throughout all three experiments, the small area between the device columns or the area around it was where the bond failed. All the averages for each test fell within a range of 40 to 50 psi with a slight negative trend in the data. However, a one-way ANOVA test yielded no significant difference between the 15, 30, and 45s parameters, p=0.58. Test 3 of the 45s parameter yielded a value of 22.82 psi which appears to be an outlier and skewing the mean. More tests could be conducted to represent the 45s O2 plasma exposure time parameter more accurately. The averages and standard deviations of these tests for each parameter were compiled and displayed in Figure 2.
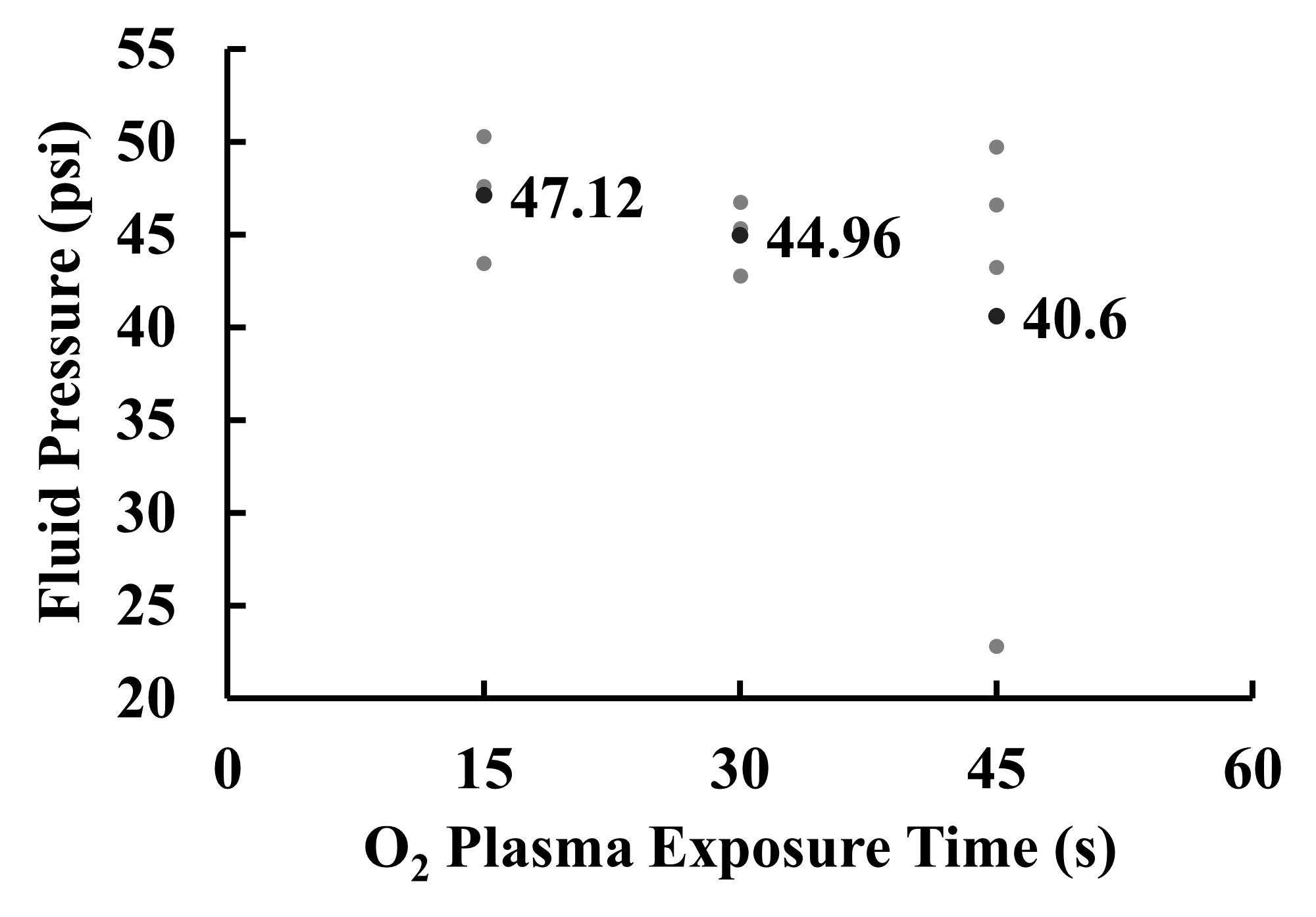
Simulation of Varied Operating Conditions Results.
For operating conditions, 3 tests were conducted for each clamp force that was set. Clamp forces of 0, 0.92, 8.10, 15.3, and 25.4 lbs were tested. Additionally, 3 tests were conducted to determine the clamp force at which the device’s integrity failed without the flow of liquid. Clamp force was continually increased until the device failed at a certain number of lbs of force. This was done to create a range of force that could be applied to a device before fluid pressure was lost due to the device’s integrity failing. The average force was calculated at 25.4 lbs. The averages calculated in this experiment all fell below 30 psi with 15.3 lbs of force being the closest. A slight positive trend is visible in the data showing that as force in lbs increases, fluid pressure capacity slightly increases. At a value of 25.4 lbs of pressure, the integrity of the device fails, and fluid pressure is lost. The averages and standard deviations of all these tests were compiled into Figure 3.
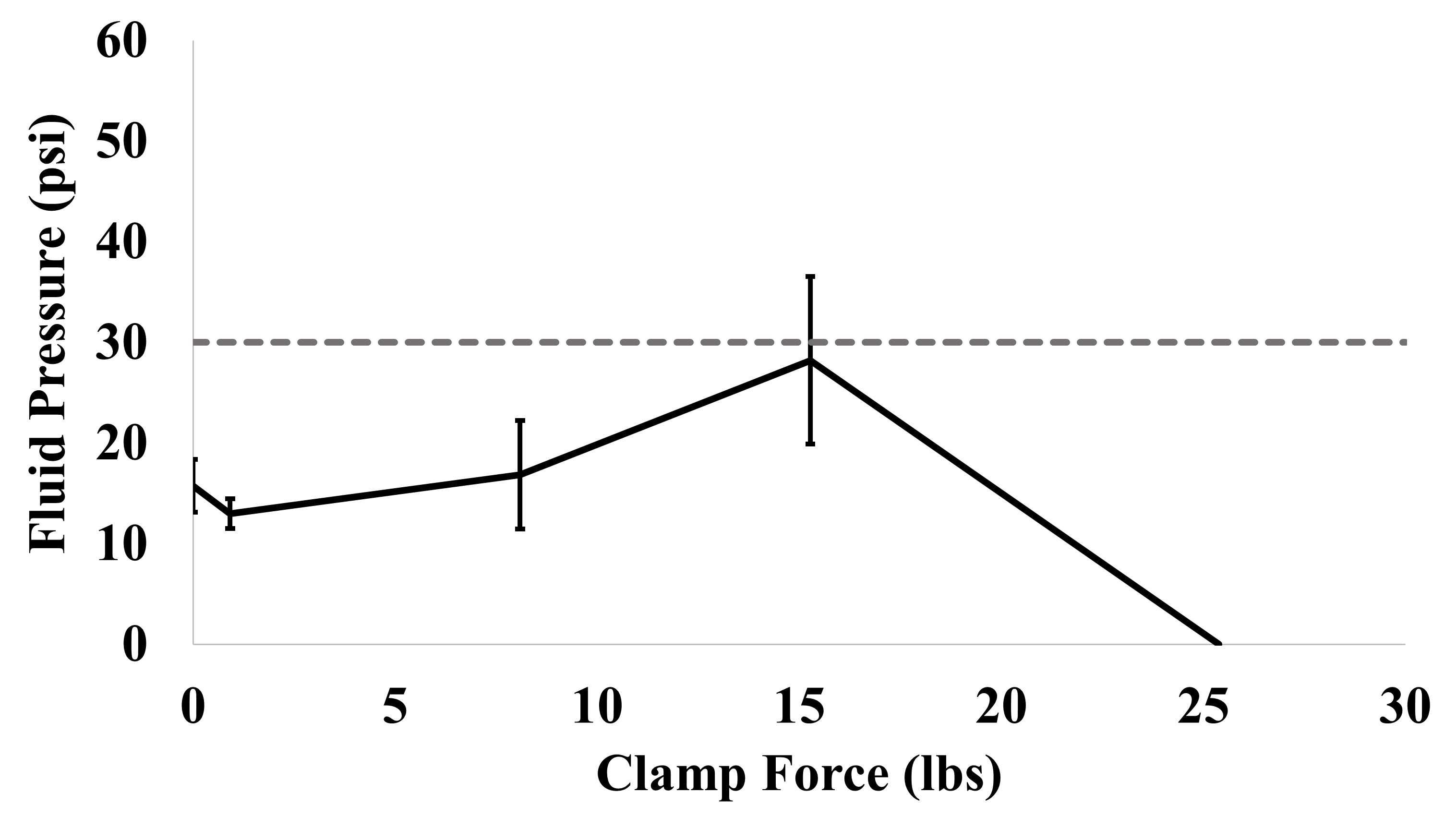
Varying Ethanol Exposure Results.
Three tests were conducted with ethanol as a substitute for pure water. In addition, data collected from the previous two experiments was compiled into a graph for comparison. The average of all the data points in each experiment was calculated and used to represent 3 categories: pure water (experiment 1), pure water packed (experiment 2), and ethanol (experiment 3). The data compiled from experiment 1 were data points from tests using pure water as the fluid passed through an unpacked column. The data compiled from experiment 2 were data points from tests using pure water as the fluid passing through a packed column. There is a significant negative trend visible in the data that suggests that ethanol exposure negatively influences total fluid pressure capacity. A one-way ANOVA test yielded a significant difference between the ethanol, pure water, and pure water packed parameters, p<0.0001. The averages and individual data points of all 3 experiments were compiled into Figure 4.
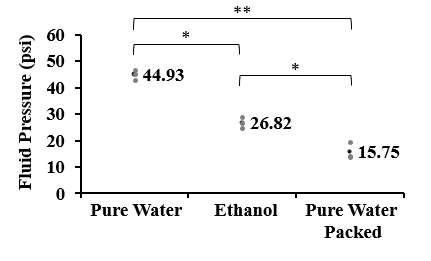
DISCUSSION.
The results of experiment 1 suggest that manipulating O2 plasma exposure time does not significantly increase the bond strength of RAPID devices. Unlike Bhattacharya in 2005, the results of this experiment suggest that O2 plasma exposure time has little effect on device bond strength. Both experiments used the pressure at which the PDMS separated from the second material as a gauge of bond strength. However, this study used pressure generated by ethanol and water rather than pressure generated by the flow of nitrogen. This is because RAPID devices utilize liquids to synthesize radiotracers. Thus, the use of ethanol and water is more appropriate for this study. The results of Bhattacharya’s study found that manipulating O2 plasma exposure was effective at increasing bond strength whereas the results of this study contradict this finding. For O2 plasma exposure time, the averages of each test were within the 40 to 50 psi range. As observed in Figure 2, there seems to be a trend in the data with a slight decrease in bond strength as exposure time is increased. The 45s exposure time parameter was the lowest and supports this observation. However, the standard deviation of the data for 45s is much larger than the other groups and suggests that the data is skewed by the value of 22.82 psi recorded in test 2. In addition, an ANOVA test revealed no significant difference despite the slight negative trend visible. This suggests that increasing or decreasing O2 plasma exposure time does not significantly affect the bond strength of RAPID devices. The O2 exposure times of 15, 30, and 45 seconds were chosen to test both above and under the initial 30s parameters used previously. Increasing the amount of exposure was thought to potentially increase the surface activation of the PDMS and glass, thus strengthening the bond. However, overactivation can occur if the PDMS and glass are exposed for too long thus weakening the bond. Considering that no significant effect was observed, further decreasing exposure time will lead to not enough activation and increasing it will lead to overactivation. Therefore, the O2 exposure time currently used to make RAPID devices is the most optimal.
The results of experiment 2 suggest that increasing clamp force on RAPID devices during operation minimally increases fluid pressure capacity. As observed in Figure 3, as clamp force increased, fluid pressure capacity increased slightly. However, the total increase in fluid pressure capacity was only 10 psi. This suggests that increasing the clamp force on RAPID devices minimally increases the total fluid pressure capacity. Additionally, the target of this experiment was 30 psi. The value of 30 was chosen because water will be heated up to 100℃ during some synthesis processes. When water reaches 100℃, its vapor pressure is 14.7 psi. By doubling this value, the safe use of this device is ensured. Unfortunately, none of the averaged data points reached this 30 psi mark.
The results of experiment 3 suggest that ethanol weakens bond strength because the average fluid pressure capacity of devices exposed to ethanol rather than pure water, is significantly lower. In Figure 4, the average fluid pressure capacity observed in experiment 1 was between the 40 to 50 psi range. The ethanol average was within the 30 to 20 psi range, showing significantly lower fluid pressure capacity. A one-way ANOVA test yielded a significant difference between the data sets suggesting that the negative trend observed is accurate. A series of t-tests were conducted to determine if there were significant differences in the sets of data. A t-test between the pure water and ethanol data sets revealed a significant difference (p = 0.014). This suggests that when exposed to ethanol, the bond strength of the device is weakened due to the difference in average fluid pressure capacity between the two conditions. A t-test between the pure water data set and pure water packed data sets revealed a significant difference (p = 0.010). This suggests that the exposure of the device to ethanol during the packing step is weakening its bond strength due to the difference between the average fluid pressure capacity. Finally, a t-test between the ethanol and pure water packed data sets revealed a significant difference (p = 0.006). This suggests extended exposure to ethanol during packing severely damages the bond strength. This supports the conclusion that ethanol is significantly weakening the bond strength of RAPID devices. A suspected reason for this is that the swelling of PDMS caused by ethanol is causing it to detach from the device resulting in a weaker bond [6]. Throughout all 3 experiments the bond failed between the device columns and the sides near the edge of the device. This result suggests that changes in the device’s design could be made to prevent certain areas from being weaker than others.
CONCLUSION.
In this study the bond strength of RAPID devices was tested under different fabrication procedures, operating conditions, and ethanol exposures. This was done through a series of burst tests that used fluid pressure capacity (psi) as a gauge for bond strength. In addition, parameters regarding the fabrication procedure, operating conditions, and ethanol exposures were manipulated. O2 plasma exposure time was manipulated to determine the optimal conditions for bond strength. Operating conditions were mimicked using the presence of a packed column, fluidic interface, and varied clamp force on devices. Ethanol exposure was manipulated by exposing unpacked devices to ethanol, pure water, and pure water with a packed column. The results of the study found that the fabrication procedure is within a robust window, clamping the fluidic interface minimally increases fluid pressure capacity, and ethanol is significantly weakening the bond strength of RAPID devices. The results of this study contribute to the development of the RAPID microfluidic device used for radiotracer synthesis in an on-demand platform. The development of this platform will increase the affordability of effective radiotracers and thus the early diagnosis and prevention of thousands of cancer related deaths globally.
Ethanol was found to have a profound effect on RAPID devices. The fabrication of RAPID devices requires an essential packing step that utilizes ethanol. Thus, the development of RAPID devices for radiotracers synthesis faces a dilemma due to the necessity of this harmful packing step. However, instead of trying to eliminate ethanol from the packing process, its effects could be minimized through diluting ethanol solutions used. In this study a 70 percent ethanol solution was used to pack columns. Potentially, a study could be conducted reviewing the effects of ethanol at lower dilutions on the bond strength of RAPID devices.
ACKNOWLEDGMENTS.
A special thanks to Mark Mc Veigh, Dr. Leon Bellan, and the REHSS program for their contributions and involvement in this study.
REFERENCES.
- 1. C.-C. Lee, G. Sui, A. Elizarov, C. J. Shu, Y.-S. Shin, A. N. Dooley, J. Huang, A. Daridon, P. Wyatt, D. Stout, H. C. Kolb, O. N. Witte, N. Satyamurthy, J. R. Heath, M. E. Phelps, S. R. Quake, H.-R. Tseng, Multistep Synthesis of a Radiolabeled Imaging Probe Using Integrated Microfluidics. Science 310, 1793–1796 (2005).
- M. Mc Veigh, L. M. Bellan, Microfluidic synthesis of radiotracers: recent developments and commercialization prospects. Lab Chip 24, 1226–1243 (2024).
- X. Zhang, F. Liu, A. C. Payne, M. L. Nickels, L. M. Bellan, H. C. Manning, High-Yielding Radiosynthesis of [68Ga]Ga-PSMA-11 Using a Low-Cost Microfluidic Device. Mol Imaging Biol 22, 1370–1379 (2020)
- 1. X. Zhang, F. Liu, K.-A. Knapp, M. L. Nickels, H. C. Manning, L. M. Bellan, A simple microfluidic platform for rapid and efficient production of the radiotracer [18 F]fallypride. Lab Chip 18, 1369–1377 (2018).
- S. Bhattacharya, A. Datta, J. M. Berg, S. Gangopadhyay, Studies on surface wettability of poly(dimethyl) siloxane (PDMS) and glass under oxygen-plasma treatment and correlation with bond strength. J. Microelectromech. Syst. 14, 590–597 (2005).
- E. J. Kappert, M. J. T. Raaijmakers, K. Tempelman, F. P. Cuperus, W. Ogieglo, N. E. Benes, Swelling of 9 polymers commonly employed for solvent-resistant nanofiltration membranes: A comprehensive dataset. Journal of Membrane Science 569, 177–199 (2019).
Posted by buchanle on Friday, June 20, 2025 in May 2025.
Tags: microfluidic, Radiotracer, RAPID